Tiempo de endurecimiento del hormigón grado 300. ¿Qué tan rápido se seca la mezcla de hormigón?
El hormigón se utiliza mucho en la construcción debido a sus características operativas: es duro, resistente al desgaste y duradero. Para obtener estas cualidades, las estructuras deben fundirse utilizando una tecnología especial. Si se violan las reglas para colocar la solución, el elemento no adquirirá las características esperadas. ¿Cómo utilizar correctamente el hormigón, cuánto tiempo tarda en secarse este material y de qué depende este parámetro?
Composición del material
Cualquier solución de hormigón consta de una mezcla de arena, cemento y agua. Dependiendo del tipo de solución, se añaden varios rellenos a los componentes principales:
- Piedra triturada, grava.
- Arcilla expandida.
- Escoria.
- Poliestireno.
- Astillas de madera o aserrín.
El tiempo de endurecimiento de la masa depende del tipo de aglutinante con el que está fabricado el hormigón. El tiempo que se seca la mezcla se determina mediante pruebas de laboratorio, luego el período obtenido como resultado de la prueba se utiliza en la práctica durante la construcción de instalaciones.
Tipos de aglutinantes
El tiempo que tarda el hormigón en secarse depende de las características del componente principal. Existen varios tipos de aglutinantes que forman la base de la solución:
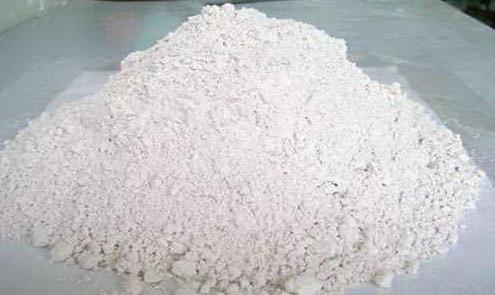
Factores determinantes
Además del tiempo medio de endurecimiento establecido de la mezcla de hormigón, el tiempo de endurecimiento se ve afectado por:
- Humedad del aire. El proceso de endurecimiento es una reacción química entre el aglutinante y el agua. En consecuencia, tan pronto como se acabe el líquido en el cuerpo de la estructura, esta acción se detendrá. Para evitar la deshidratación y el agrietamiento del volumen de hormigón, es necesario crear una condición de humedad suficiente de al menos el 75%.
- Temperatura ambiente. Dado que el agua interviene en la reacción, es necesario evitar que se congele durante la estación fría. Durante el proceso de endurecimiento, la estructura libera calor; a temperaturas elevadas, la interacción de los componentes se produce notablemente más rápido.
- El tipo de aglutinante y la cantidad de agua en la solución también determinan cuánto tiempo debe secarse el concreto. El yeso en polvo, con una cantidad suficiente de líquido, adquiere una estructura sólida en un par de horas, el cemento Portland requiere entre 12 y 16, dependiendo de las condiciones enumeradas.
- El espesor de la estructura afecta el endurecimiento general de la solución.
Estos factores deben tenerse en cuenta al diseñar obras de construcción en las que se utiliza hormigón. El tiempo que tarda una estructura en secarse depende del entorno y cuidado apropiado más allá del volumen especificado.
Términos promedio
Muy a menudo, para la construcción de estructuras críticas, se utiliza el clásico. cemento concreto. El tiempo que se seca una estructura hecha a partir de él se determinó mediante investigaciones en un sitio de construcción y en un laboratorio:
- En 3 días, la solución adquiere aproximadamente el 30% de la fuerza inherente a la marca, siempre que alta humedad y temperatura del aire no inferior a 15 0 C.
- De 7 a 14 días, el hormigón adquiere una dureza suficiente para el movimiento humano hasta un 80% de sus características previstas.
- 28 días es un período fijo para tener la fuerza incorporada completa. Durante este período, la instalación puede funcionar a máxima velocidad.
- El hormigón se distingue de otros materiales por su capacidad de aumentar sus características durante el período de funcionamiento. Se observó que después de 90 días el cálculo supera los parámetros establecidos en un 20%.
La influencia del encofrado: sí o no
Al construir cualquier objeto, el método se utiliza a menudo. construcción monolítica. Surge la pregunta: ¿cuánto tiempo se seca el hormigón en el encofrado? ¿Afecta esto al tiempo de endurecimiento de la estructura?
El proceso de solidificación no es más que reacción química. Sólo las condiciones externas pueden influir en su velocidad: la temperatura y la humedad del ambiente y algunos catalizadores, aditivos que se introducen en la mezcla durante la producción para obtener y mejorar ciertas cualidades del material.
Utilizado para encofrado tablas de madera, láminas metálicas y contrachapados de construcción. Estos materiales están diseñados para fijar la forma de la futura estructura. Son capaces de retener parcialmente el calor en el volumen que se solidifica, pero no en cantidades tales que se produzca una aceleración significativa de los procesos.
Con el cuidado adecuado, el hormigón del encofrado endurece en un plazo determinado por las condiciones de temperatura:
Temperatura, 0°C | Tiempo de fraguado, días |
25…30 y más |
Transcurrido el plazo indicado, se retira el encofrado, la estructura continúa endureciéndose por sí sola, mientras continúan los trabajos de instalación en la construcción de la instalación.
Dependencia del tiempo del volumen.
Las estructuras de hormigón monolíticas tienen diferentes dimensiones. Los cimientos para edificios y estructuras se realizan en varias configuraciones: listón, pilote, losa. Sus cuerpos tienen diferentes volúmenes.
Para saber cuánto tiempo tarda en secarse una base de hormigón, debes centrarte en el grosor de la estructura. Dado que el endurecimiento y la solidificación son reacciones químicas, deben ocurrir de manera uniforme en todo el volumen. Cuando se produce la petrificación, se libera calor. En consecuencia, la parte interna del elemento alcanza más lentamente su estado final. Además, en las capas superiores, el exceso de líquido se evapora más rápido y el material adquiere la estructura suficiente para continuar. trabajo de instalación.
Estructuras particularmente gruesas como cimientos de losa para grandes estructuras, piscinas, centros comerciales, pueden resistir desde tres meses hasta que todo el volumen de la base vertida alcance el estado de diseño.
Cómo aumentar la velocidad de endurecimiento.
Hemos determinado cuánto tiempo tarda el hormigón en secarse en el exterior en condiciones normales. Ahora veamos qué métodos se pueden acelerar este proceso:
- Se debe mantener un nivel constante de humedad inmediatamente después de colocar la mezcla de hormigón en el encofrado. Para ello, los formularios rellenos se cubren con material impermeable (película o lona) y se riegan constantemente.
- Crear condiciones de temperatura de trabajo es importante para la construcción en invierno. Como saben, durante las heladas, el agua cristaliza y se expande, lo cual es inaceptable en una estructura endurecida. Para evitar esto, en periodo de invierno la estructura del encofrado se calienta artificialmente para acelerar los procesos químicos. Además, durante la producción, se añaden catalizadores especiales a la mezcla para promover un fraguado uniforme y rápido de los componentes.
- El cálculo correcto de la proporción de agua y cemento asegura el endurecimiento oportuno de la mezcla sin la necesidad de una expulsión adicional del exceso de agua.
Durante los trabajos de construcción en Area suburbana A menudo se utiliza hormigón. Parecería que sería muy complicado: preparar un agujero, encofrar, mezclar el mortero y verterlo, eso es todo lo que se necesita para una construcción exitosa. Sin embargo, la cosa no termina ahí. Es después de verter que es necesario controlar y cuidar cuidadosamente la solución. Es necesario conocer el tiempo de secado para poder cuidarlo adecuadamente.
Diagrama de piso.
Si no cuida el mortero vertido y distribuido, entonces la base de la cerca o los cimientos, los caminos, todo puede agrietarse, lo que, en consecuencia, reducirá la resistencia del material varias veces.
Cuidado
El cuidado de la solución implica una amplia gama de medidas específicas con las que se pueden crear las condiciones más óptimas para el envejecimiento de este material. Esto le permitirá adquirir la fuerza declarada específicamente para esta marca.
El cuidado se lleva a cabo para:
- minimizar la contracción de la solución;
- ayudar a que la estructura adquiera la resistencia necesaria en un corto período de tiempo para un funcionamiento más prolongado;
- proteger la solución de la deformación debido a los cambios de temperatura;
- evitar el secado prematuro o daños.
Para realizar el mantenimiento oportuno del mortero de cemento colocado, debe comenzar inmediatamente después de colocar el mortero en el encofrado.
El primer paso es inspeccionar cuidadosamente el propio encofrado para evaluar la seguridad de las dimensiones planificadas y excluir fugas o roturas. Sin embargo, si se encuentran defectos, deben eliminarse inmediatamente lo antes posible. En una o dos horas se pueden corregir por completo.
Diagrama de diseño estructural.
- para que la solución obtenga la resistencia requerida, es necesario protegerla tanto como sea posible de diversos impactos o cualquier otra influencia mecánica;
- como regla general, para evitar grietas, inmediatamente después de la colocación, cubra la superficie del mortero de cemento colocado con una película plástica o un paño húmedo;
- Al principio, durante uno o dos días, es necesario intentar mantener el régimen de humedad. Cabe recordar que la humedad normal cuando la solución se seca es del 90-100%. En otras palabras, las estructuras de cemento requieren un exceso de agua.
¿Qué puede resultar si no se mantiene la humedad requerida al secar la mezcla de concreto?
- En primer lugar, el hormigón por sí solo no adquirirá la resistencia necesaria.
- Además, estará sujeto a la descamación de la arena contenida en la mezcla y, como resultado, a una mayor absorción de agua. Este hormigón presenta poca resistencia a las influencias atmosféricas y químicas. Dicho material puede desarrollar grietas debido a una contracción prematura.
El hormigón recién colocado tiene un volumen mucho mayor que el mismo hormigón secado.
Por este motivo, el hormigón recién colocado necesita la máxima humedad, para que vaya reduciendo gradualmente su volumen hasta el estado necesario sin provocar deformaciones.
Si la solución de cemento no recibe el porcentaje requerido de humedad, surgen en ella las llamadas tensiones estructurales o internas, por lo que pueden aparecer grietas.
El primer signo de falta de humedad son las grietas superficiales en el producto vertido. mortero de hormigón. Si no se toman medidas, tales grietas penetrarán profundamente en el hormigón, privando de resistencia a la mezcla vertida.
- El tiempo de secado también se ve afectado por las diferentes precipitaciones climáticas: cuanto más fuerte es la influencia del sol y el viento, más rápido se seca la mezcla;
- Durante un cierto período de tiempo, el hormigón adquiere cierta resistencia. Por ejemplo, en aproximadamente 8 horas una mezcla de cemento puede alcanzar un valor de resistencia de 1,5 MPa. En este caso, es necesario humedecer bien la superficie con la solución colocada.
Bajo ningún concepto se debe pulverizar el hormigón con un chorro de agua en este momento. Es necesario regar cuidadosamente la solución vertida con riego disperso.
Diagrama de cimentación de hormigón.
Para mayor comodidad, cubra la estructura con un trapo empapado en agua, humedeciéndolo según sea necesario. Sin embargo, al humidificar, es necesario controlar la temperatura exterior.
Por lo tanto, a temperaturas inferiores a +5 °C, se debe detener el riego y cubrir la estructura lo más herméticamente posible con materiales de construcción que retengan el calor. Por ejemplo, espuma de poliestireno o lana mineral, así como trapos o aserrín.
En el caso de que sea especialmente necesario mantener una humedad constante de la solución, entonces toda la estructura debe cubrirse durante un tiempo con una película especial que tenga un espesor de al menos 0,2 mm.
Al conectar partes de la película, se colocan superpuestas de modo que los extremos se superpongan entre sí al menos 30 cm. Si es posible sellar las costuras de unión con cinta adhesiva, vale la pena hacerlo. Este tipo de "cubierta" evitará la evaporación de la humedad de la solución, manteniendo su resistencia.
Dependencia de las condiciones climáticas.
El hormigonado en diferentes condiciones climáticas requiere un cierto tiempo de endurecimiento.
Al realizar trabajos de construcción con mortero, todos los constructores notan una desaceleración en el endurecimiento, lo que significa que la resistencia de dicho mortero de cemento no aparece tan pronto.
Si la temperatura exterior no supera los +5 °C, se necesitará el doble de tiempo para alcanzar la dureza que alcanza el hormigón a +20 °C.
Si la temperatura desciende a cero, el aumento de fuerza prácticamente se detiene. La mezcla, por supuesto, se endurecerá, pero se formará en ella un sistema de poros capilares. Bajo la influencia de las heladas, toda el agua que se encuentra en los poros del hormigón puede congelarse por completo. Como resultado, el hielo resultante ejerce una fuerte presión sobre los poros de la mezcla de cemento, lo que puede destruir prematuramente la estructura de la estructura de hormigón.
Por eso, hoy en día existen tipos especiales de mezclas que son más resistentes a las heladas.
Periodo de verano
Si la construcción se lleva a cabo en un clima bastante caluroso, debe recordarse que el hormigón se endurece más rápido a altas temperaturas. La mezcla se calienta de forma natural hasta temperatura ambiente. Dicho calentamiento afecta negativamente su condición y comienza a deformarse, especialmente cerca de la superficie.
El período durante el cual pueden aparecer grietas es de 4 a 16 horas. Por tanto, es necesario utilizar cementos Portland especiales de endurecimiento rápido. Su grado de resistencia es 1,5 veces superior al habitual, lo que favorece un endurecimiento rápido manteniendo todas sus cualidades positivas.
Por lo tanto, cuando hace calor es aconsejable realizar los trabajos de construcción por la mañana o por la tarde, evitando las horas calurosas de la tarde. En condiciones de calor extremo, es necesario regar con más frecuencia el paño húmedo que cubre la estructura.
Si hablamos de tiempos de secado generalmente aceptados, este tiempo es de 28 días. Es después de este período cuando la mezcla adquiere toda su fuerza.
Sin embargo, endurece en los primeros días, dependiendo de la temperatura ambiente y de la marca de cemento utilizada en la preparación de la solución. Es en este momento cuando se produce el principal aumento de la resistencia estructural.
Por lo tanto, los trabajos de construcción pueden continuar después del endurecimiento inicial, lo que determina la vida útil máxima del hormigón vertido, ya sea la base, la base de una valla o caminos en el sitio.
Mucha gente rellena los cimientos, hormigonando el suelo o las paredes, sin recurrir a la ayuda de especialistas. Para que los esfuerzos tengan éxito, es importante tener en cuenta el tiempo de fraguado y endurecimiento del cemento, así como las condiciones que afectan la velocidad de todo el proceso.
El principal factor que afecta el tiempo que tarda en secarse una solera o base es la temperatura. Si cambia, la solución no puede fraguar bien. Después del secado en tales condiciones, la resistencia del hormigón deja mucho que desear.
En invierno aumenta el tiempo de endurecimiento del cemento. A temperaturas inferiores a 10 °C, el fraguado se ralentiza y el agua en la composición puede incluso destruirlo. Para evitar estas consecuencias, es necesario mantener constantemente el calor. Si el clima no es lo suficientemente cálido, tendrás que hacerlo tú mismo. Al construir una base con cemento Portland de grado M400 o M500, el trabajo se ahorra con encofrados o un terraplén de aserrín.
Las condiciones favorables son +22-25 °C y una humedad de aproximadamente el 65%. Si prepara cemento en el exterior, debe asegurarse de que no esté expuesto a la luz solar directa y también controlar los cambios de temperatura. También se debe evitar la falta de humedad, de lo contrario el material comenzará a desmoronarse y agrietarse.
¿Cómo hacer que el cemento se seque más rápido?
No hay necesidad de depender de las condiciones climáticas. Puede acelerar el trabajo usted mismo de la siguiente manera:
- Es necesario mantener la temperatura de 22-25 °C. Al construir los cimientos, esto se puede garantizar parcialmente con encofrados de madera y, en otros casos, con un terraplén de aserrín. También usado pistola de calor, pero sólo después de que haya pasado un día desde el momento del vertido y con precaución. De lo contrario, comienzan a aparecer grietas en el hormigón, a medida que el agua que lo compone se evapora.
- Si la finalización del trabajo está prevista antes del inicio del invierno, el primer paso en el cálculo es incluir cuánto tiempo se seca el mortero de cemento a 0 °C. A esta temperatura mezcla de concreto Se endurece sólo después de 6 a 10 horas y se endurece durante más de 28 días. Con la llegada de las heladas, los expertos recomiendan posponer la construcción hasta que termine el frío.
- Al hormigonar suelos o paredes, no es necesario aplicar una capa de mortero demasiado espesa.
- La solución debe mezclarse proporciones correctas. El cemento con arena y piedra triturada se mezcla en las siguientes proporciones: 1:3:5. Se vierten 0,68 m3 de agua por 1 m3. La mezcla debe quedar homogénea.
- Se recomienda utilizar una hormigonera. Mezcla la solución más rápido y más a fondo. Esto acelera el proceso de trabajo y mejora la calidad del hormigón.
Elección del cemento
El tiempo que tarda el cemento en secarse también se ve afectado por su composición y densidad. Las marcas de cemento Portland están marcadas con la letra M y un número, que indica qué carga puede soportar. Cuanto más densa sea la mezcla, más tardará en endurecerse. El hormigonado de alta calidad no permite la violación de proporciones al realizar la solución.
M50-M100 no son adecuados para estructuras grandes. M400 y M500 son las marcas más confiables y se utilizan para construir cimientos.
Es imposible decir exactamente cuánto tiempo tarda en secarse el cemento Portland. Es difícil de mantener durante todo el trabajo. condiciones favorables para endurecer, y esto afecta en gran medida la velocidad del proceso. El tiempo de secado aproximado para los grados M400 o M500 es de un mes.
Etapas de endurecimiento
Todo el proceso se divide en fraguado y endurecimiento de la solución.
1. En condiciones favorables, el fraguado se produce en 2 a 4 horas. En 24 horas, el cemento se endurece lo suficiente como para que una persona pueda trabajar sobre él sin dejar marcas. Después de una semana, la fuerza alcanza el 70%, y luego esta cifra se acerca gradualmente al 100%.
2. Tiempo de endurecimiento: desde varias semanas hasta 1-2 años. Todo depende de la corrección del hormigonado, así como del tipo de cemento Portland.
Al construir cualquier objeto, lo más importante es una base de alta calidad sobre la que se asienta el edificio o la casa. A menudo se utilizan mezclas de hormigón para rellenar los cimientos o losas. Para que los edificios resistan cualquier carga sobre los cimientos en el futuro, es necesario utilizar mezclas. Excelente calidad. La base vertida en sí debe estar lista para la construcción de paredes y pisos posteriores sobre ella, es decir, es necesario esperar un cierto período para que el concreto se endurezca. ¿Cómo ocurre este proceso, cuánto tiempo lleva y es posible acelerar el endurecimiento?
Las mezclas se utilizan para rellenar los cimientos de estructuras y losas de piso.
Después de mezclar cemento y agua para producir una solución, comienza una interacción compleja entre ellos, como resultado de lo cual se forma un compuesto completamente nuevo con características propias. El agua penetra gradualmente en los granos de cemento, cuyos minerales reaccionan químicamente con él. Durante esta reacción, los minerales se convierten en hidrosilicatos de potasio. Este proceso se llama endurecimiento del hormigón.
El grado de endurecimiento del hormigón se puede comprobar mediante herramientas de diagnóstico especializadas.
El endurecimiento no se completa en un día. Para que el hormigón adquiera la resistencia que necesita y deje de ser plástico se requiere de un determinado periodo de tiempo. A esto se le llama tiempo de endurecimiento. El endurecimiento puede durar años, lo que puede prolongar significativamente el proceso de construcción durante mucho tiempo. por mucho tiempo. Los constructores no pueden esperar tanto y han calculado un período de fijación de objetivos tras el cual los cimientos pueden soportar la carga de diseño.
Período de control de fraguado
Para que el hormigón alcance su resistencia a la compresión original, se necesitan condiciones favorables. Estos incluyen la temperatura ambiente y la humedad del aire.
A altas temperaturas y humedad del aire, el endurecimiento avanza más rápido y a bajas temperaturas se ralentiza. La exposición a temperaturas del aire cero y negativas puede detener el proceso de fraguado. La temperatura óptima para el endurecimiento es de 20 a 30 grados por encima de cero, la humedad del aire no debe ser inferior al 90%. En condiciones de laboratorio, se encontró que el endurecimiento más activo en las condiciones descritas ocurre en la primera semana después de su vertido. Durante este período, el hormigón puede ganar hasta un 70% de su resistencia. Alcanza el 100 por ciento de fuerza de marca 28 días después de verterlo.
Calendario de curado en función de la temperatura.
En condiciones reales, la temperatura del aire no puede ser constante: es mayor durante el día y menor durante la noche, y la humedad también cambia en diferentes momentos del día. Por ello, los expertos recomiendan esperar unos días más para levantar el edificio sobre sus cimientos. Por lo tanto, los trabajos de construcción no pueden continuar antes de un mes después del vertido.
Aunque 28 días se considera óptimo para los trabajos de construcción, en algunos casos es necesario aumentarlo. Se trata de sobre estructuras que entrarán constantemente en contacto con la humedad durante la operación. Estos son muelles, presas, presas. El endurecimiento de tales estructuras con su fortalecimiento lleva 3 meses. Como se mencionó anteriormente, el endurecimiento continúa después de 28 días y seis meses. Sin embargo, este proceso es mucho más lento que las etapas iniciales de fraguado y garantiza la fiabilidad de estructuras que se vuelven aún más duras y resistentes con el tiempo.
Mantener la fuerza de la mezcla
Para que el hormigón sea más resistente debe secarse uniformemente en todo su volumen, por lo que las estructuras deben humedecerse constantemente en toda la superficie.
Para que se produzca la reacción química dentro de la solución es necesario un líquido, porque el fraguado se produce gracias al agua. Pero como el proceso de endurecimiento dura más de un día, el agua puede simplemente evaporarse. Para que esto no suceda, la superficie de la estructura debe regarse y luego cubrirse con una película o material para techos. El hormigón debe humedecerse constantemente, especialmente durante las estaciones cálidas y secas. Si hace viento, las esquinas y la superficie de la base expuesta se secarán más rápido que el resto del interior. Pero para que el hormigón sea más resistente, debe secarse uniformemente en todo su volumen.
Cabe recordar que el hormigón durante el proceso de endurecimiento cambia de volumen y se contrae. La contracción se produce más rápidamente en las capas superficiales de la base. Si no le proporciona suficiente agua, se formarán grietas por contracción en la superficie, cuya apariencia reducirá la resistencia y durabilidad de la estructura.
En la construcción industrial estructura de concreto Durante su maduración se calienta constantemente. Se recomienda a los propietarios privados no verter hormigón en climas fríos.
En la estación fría, no es deseable verter los cimientos de hormigón de su propia casa o de cualquier edificio en trama personal. Esto se debe al hecho de que el agua contenida en la solución puede simplemente congelarse. Al congelarse, aumentará de volumen y comenzará a destruir el hormigón desde el interior, y su endurecimiento se detendrá. Si la temperatura del aire es inferior a 10 grados, el proceso de endurecimiento será muy lento. En la construcción industrial, una estructura de hormigón se calienta constantemente durante su maduración, por lo que los trabajos de vertido de cimientos se pueden realizar en cualquier época del año. Pero se recomienda a los propietarios privados que construyan los cimientos solo en verano, cuando la temperatura del aire es de más de 20 grados o más.
Acelerando el proceso
28 días es el tiempo de control del endurecimiento del hormigón. Pero en algunos casos es necesario que el proceso de fraguado del hormigón avance más rápido. Esto se aplica a los trabajos realizados en invierno, o al desmolde necesario de objetos en fechas tempranas. En tales casos, puede acelerar el proceso de endurecimiento decenas de veces. Debido a que el concreto madura más rápido a altas temperaturas y humedad, el método más común de aceleración en fábrica es esterilizar en autoclave o vaporizar la losa de concreto.
En un autoclave, la placa se cuece al vapor a alta presión. Como resultado, en sólo 15 horas el hormigón alcanza la resistencia de un año de maduración.
Se coloca en una “sala de vapor” de autoclave, donde en un ambiente húmedo la placa se cuece al vapor a alta presión. Como resultado de este tratamiento con vapor, en 15 horas el hormigón alcanza la resistencia equivalente a un año de maduración en condiciones naturales. Y aunque después del tratamiento térmico en autoclave la losa de fábrica ya no ganará resistencia, su calidad no es en modo alguno inferior a la del hormigón que se ha endurecido de forma natural.
Para acelerar el fraguado se utilizan sustancias especiales que se añaden a la mezcla. Composición requerida y la cantidad de aditivos se determina experimentalmente en laboratorios de construcción. Los aceleradores como porcentaje de la masa total de cemento no deben exceder las cifras establecidas por los laboratorios. Entonces, no se permite agregar más del 4% de sales. Ácido nítrico, 2% sulfato de sodio y 3% cloruro de calcio.
El sulfato de sodio se puede utilizar incluso en estructuras de hormigón armado, que están diseñados para operar en áreas expuestas a corrientes parásitas. Es extremadamente indeseable agregar otros aceleradores al cemento de alúmina o al mortero de estructuras reforzadas con acero prerreforzado a altas temperaturas. Si se utilizan aceleradores junto con el autoclave, esto reducirá aún más el tiempo que lleva endurecer el concreto. Los cementos Portland comunes pueden acelerar el proceso de endurecimiento si se les agrega una amoladora vibratoria húmeda o seca (cemento fino). Actualmente, también se producen mezclas especiales de hormigón de endurecimiento rápido.
En el mercado materiales de construcción Existen muchos aditivos diferentes para morteros de hormigón. Algunos de ellos solo son capaces de acelerar el endurecimiento, otros tienen una amplia gama de funciones y no solo son aceleradores, sino también plastificantes e incluyen componentes anticongelantes. Los precios de los suplementos dependen de la complejidad de obtener los componentes incluidos en su composición y de su cantidad. El costo está influenciado por el lugar donde se fabrican los aceleradores. Los precios de los aditivos rusos son más bajos que los de sus análogos importados. El cloruro de calcio granulado y el plastificante-acelerador Fort “UP-2” serán más baratos, comprar nitrato de calcio seco y kratasol-UT costará más.